Introduction of the DFMA software (Boothroyd Dewhurst) with practical example (turbine)
Dear readers, my previous article was on Should Costing, it’s approach, benefits and cost saving opportunities using Boothroyd Dewhurst Inc. DFMA software.
In this article, I would like to elaborate in detail about Boothroyd Dewhurst Inc. DFMA software and Case studies.
I would like to comment on the following points.
- What is DFMA Boothroyd Dewhurst Software all about
- DFM Software Capabilites
- Benefits of using DFM Concurrent Costing software.
- Case Study
- Conclusion
What is DFMA Boothroyd Dewhurst Software all about?
DFMA® is the combination of two design methodologies: Design for ease of Assembly and Design for ease of Manufacturing. Design for Assembly results in reduced product cost through the use of fewer, multi-functional parts compared to conventional designs. Design for Manufacturing results in reduced part costs through analysis of the primary cost drivers for a given manufacturing process method.
DFM Concurrent Costing software provides an immediate, thorough understanding of the primary cost drivers associated with manufacturing your product – and establishes a benchmark for what your product „should cost.“ Additionally, DFM guides you through an assessment of alternative processes and materials to help you generate various design proposals. Cost results update automatically as you specify tolerances, surface finishes, and other part details. Gradually, as you choose effective shape-forming processes and consider how to modify part features to lower cost, your product becomes cost optimized.
Figure 1: Excerpt from the user interface of DFMA (Boothroyd Dewhurst)
What software products have you developed?
The DFMA® software constitutes DFA: Product Simplification and DFM: Concurrent Costing®. They function together but are installed as separate modules.
What industries/products does DFMA® work best with?
DFMA® can be applied to any electro-mechanical product that requires manufacture and assembly of metallic or plastic components. Ignoring any cultural/organizational challenges, there is no evidence that DFMA® is better suited to any particular industry.
Is DFA (Design for Assembly) an exercise in Value Engineering?
While there are similarities between these two methodologies in that they both involve function and cost, it is intended that total product functionality be static during a Design for Assembly exercise. To achieve cost reduction through Design for Assembly, the use of fewer, multi-functional parts in place of more complicated assemblies is encouraged. Value Engineering differs in that product functionality is analyzed in terms of value delivered by its inclusion in the product. In Design for Assembly, we are only focused on impacting the product’s assembly efficiency while maintaining all of the functionality the designer intended.
DFM Software Capabilites
The Major Manufacturing Cost Models are:
- Assembly Fabrication, Automatic Assembly, Blow Molding, Die Casting, Plastic Extrusion, Hot Forging, Injection Molding, Investment Casting, Machining, PCBA, Sand Casting, Sheet Metal, Foam Molding, Thermoforming, Custom User Processes, and many others fully included.
It has fully Populated Operations, Machine, and Material Libraries.
You get a Cost Breakdown, Cost vs. Life Volume Graphs.
With the Machining Quick Estimator you get an accurate result in minutes.
With the Manufacturing Profile you can Compare costs across different regions or suppliers.
They have an On Context Help System and integrated CAD Support. You can select features directly from the model. It supports STL, STEP, IGES Formats.
Benefits of using DFM Concurrent Costing Software
A Highly Accurate Cost-Estimator
Thanks to over 40 years of industry experience, DFM consistently provides accurate feedback on the change in cost associated with changes in parts or their design. Parts that are more expensive to produce than others will always yield higher cost estimates, and the amount of added expense is always correctly portrayed in the DFM results, something that historical pricing and automated CAD analysis cannot do. Our approach to cost analysis provides superior accuracy because it correctly identifies each step required to manufacture the part and then quantifies each associated cost.
An Easily Implemented Solution
DFM software delivers complete and accurate should-costing capability right out of the box. By contrast, many cost estimating packages require months or even years of expensive consulting to build custom templates for the user. These templates attempt to manually fix cost result errors the software makes, a process which inadvertently causes other cost results to become incorrect. DFM software avoids this inflexible approach, instead using a solid understanding of cost drivers to quickly and effectively tell you what your parts really cost to make.
An Aid to Concurrent Engineering
DFM shortens the product development cycle by providing early-stage cost transparency between design, manufacturing, marketing, finance and purchasing personnel. The ability to share cost information during early stages prevents many of the hurdles that the typical product development team encounters when trying to get a product to the market.
A Useful Design Tool
Rather than simply providing cycle time and cost estimates, a DFM analysis educates the designer on the most important cost drivers of the proposed design. The availability of this information is invaluable when deciding how the design should be changed to reduce cost. As soon as improvements are identified, new DFM estimates can instantly be generated to get accurate results for alternative proposals.
An Effective Supplier-Negotiating Aid
Thanks to reliable accuracy and transparency, DFM serves as a highly effective procurement tool. The software reports all of the values and assumptions that are used to generate a cost estimate. This offers a purchasing department far more negotiating leverage than a basic quote could ever provide. With DFM, supplier negotiation is about sharing relevant data instead of using pressure tactics to lower price.
A Competitive Benchmarking Tool
DFM allows you to benchmark a competitor’s product even when CAD models or supplier information isn’t available. An understanding of what the competing product “should cost” is gained and can be compared with the cost results for your own design. With DFM, a strategic advantage is achieved because the market feasibility for your products can be evaluated while considering the cost of your competitor’s products.
The Link to Design for Assembly
DFM complements Design for Assembly (DFA). Engineers use DFA to reduce the assembly labor within a product through the consolidation of single function parts into more elegant, multifunctional designs. The DFM software is then used to help the design engineer quickly compare the costs to produce each alternative design. Used together, the DFM and DFA software give engineers an early cost profile for each product design and provide a basis for planning and decision making. Such analyses, when performed at the earliest stages of concept design, have the potential to greatly influence manufacturing and other life cycle costs before they are solidified and become locked in place.
Case Study Turbine Exhaust
Here is a brief insight into the outputs.
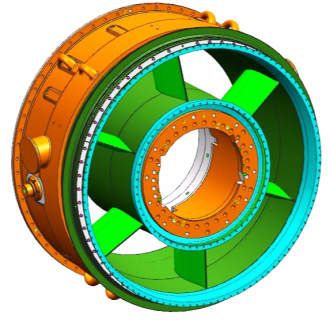
Objective: To carryout should costing
Inputs:
Annual Volume: 4 Nos.
Envelope Dimension : 2022 x 2022 x 900 mm
Weight : 5538 Kg
Number of parts : 68
Should cost Results
- Should Cost : € 26,462
Cost model summary – Break up of Individual process cost as against Material, Setup, Process, Rejects, and assembly.

Detailed Cost breakup of Sub assembly parts and Secondary operations.
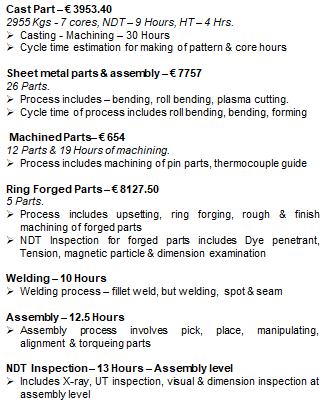
Please contact us if you would like more case studies.
Conclusion
Should cost calculations can be carried out using Boothroyd Dewhurst DFMA tool for complex assemblies which includes various secondary operations and cost breakdown of each operations can be utilized for supplier negotiations.
Should Cost analysis using BDI DFMA tool provides a better insight for the sourcing team to identify the supplier’s profit margins and grab the purchasing power from the supplier It helps them in identifying the key cost drivers of the product and helps in “make or buy” decisions Infer price comparisons of the part, assembly, if outsourced to different geographical locations For any strategic sourcing, should-cost analysis would be an ideal tool for making profitable negotiations It also aids new product development team to evaluate the product cost in the early stage of development. Engineers will have a better insight of cost implication on the design and revisit on design to- cost Analyse viable alternate material or process to study the cost behaviour and make necessary trade-off Identify the apt materials and processes in the early stages and avoid design iterations in the later stage Should-cost results will help in understanding the supplier quotient and their strengths.
Thank You! Your read the articel Introduction of the DFMA software (Boothroyd Dewhurst) with practical example (turbine).